Controlling product quality is critical in ensuring customer satisfaction, brand reputation and reducing the risk of product recalls. Here are some steps how we control product quality:
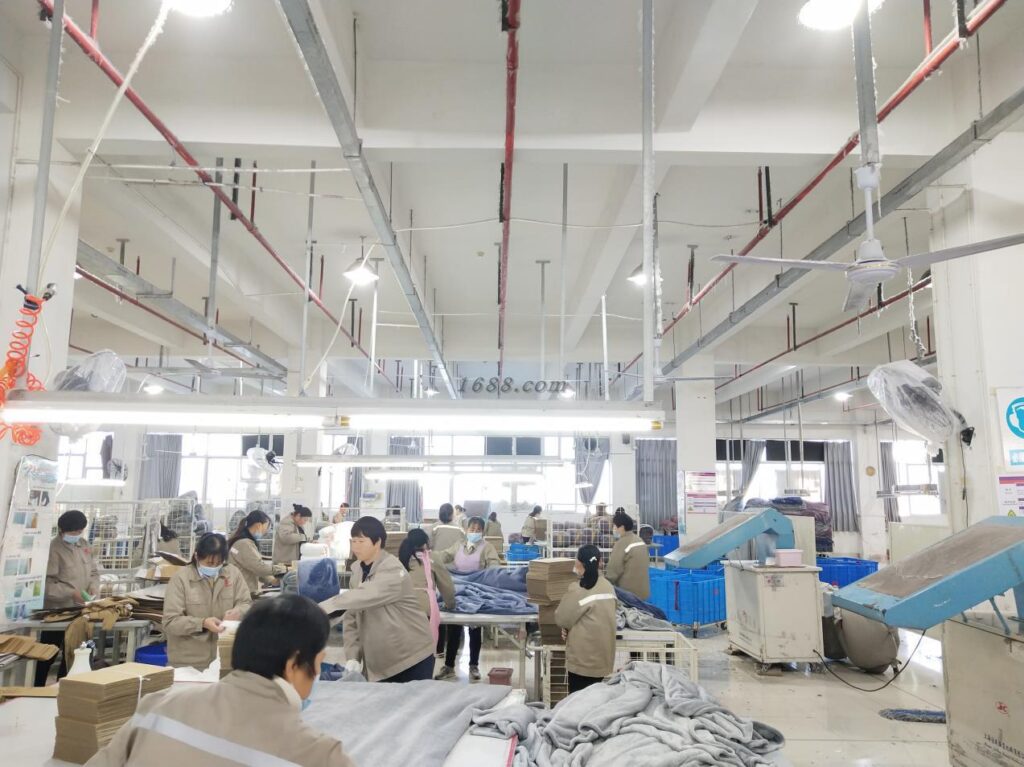
- Define Quality Standards and Specifications: First, establish quality standards and specifications that our products must meet based on customer requirements and industry standards. This will serve as a reference for product development, manufacturing and quality control.
- Perform Quality Inspections: Plan and perform quality inspections at different stages of production to ensure consistency and detect any defects or issues early. During Cutting Fabric, our team will inspect fabric, if there is any default fabric, we will cut fabric out.
- Train Employees: We also Provide training to employees involved in production and quality control to ensure they understand quality standards and procedures. espencially the packing employees. Make sure they are quite familiar with every quality standards.
- Perform Regular Audits: Conduct regular audits to ensure that quality control processes are being followed and to identify areas for continuous improvement.
- Communicate with Customers: We always Listen to customer feedback and promptly address any issues or concerns. This can help catch quality issues early and prevent larger problems.